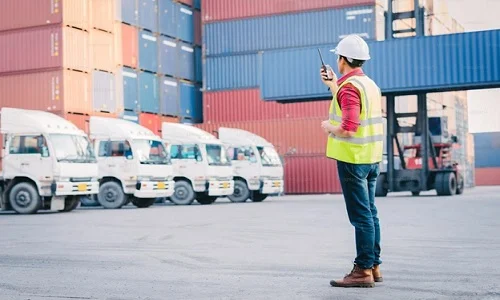
In an increasingly competitive and globalized business environment, supply chain risk management has become a strategic imperative for companies. Linked supply networks span countries and time zones, integrating operations over long distances. While this scope allows for cost savings and economies of scale, it also opens up new vulnerabilities.
Disruptions from unpredictable events are becoming more common and more serious. What happens at any single point of failure can now easily resonate throughout the system. Because supply chains have so many moving parts and interdependencies, they need more of a safety net. As a result, businesses are much more exposed to supply and demand uncertainties.
This paper outlines in more detail the five foundational elements upon which successful supply chain risk management practices are built.
1. Ensuring Compliance
Risk management ensures strict conformity across the supply chain. This means that rigorous systems and protocols of monitoring providers to confirm that they adhere to all relevant laws, rules, and benchmarks could reduce enormous risks that can cause interruptions in operation.
Similarly, redundant auditing and certification processes should highlight any non-compliance issues in good time. In this way, the organizations can fix problems by working with providers to rectify them before they spiral out of control.
Compliance fully mitigates legal and regulatory risks that expose the organization to fines, penalties, or termination of services. This means that assurance is provided for the continuation of Supply Chain Risk Management once every level is sanctified to hold ground on adherence to best practices.
Compliance also strengthens the Supply Chain. The evaluation and accreditation process for new suppliers with stringent parameters helps normalize resources. Even while perpetual compliance ensures the survival of the supplier base for a long time, the identification of suppliers conforming to the best standards facilitates traceability.
2. Comprehensive Visibility
Lack of end-to-end visibility into the supply chain is a significant risk. Companies often do not have a clear line of sight into their extended global networks, which may include multiple tiers of suppliers, vendors, facilities, and distribution channels. Therefore, limited visibility closes their eyes to potential risks and vulnerabilities.
The first pillar for effective risk management is comprehensive visibility into the complete supply chain. Firms must map out their entire supply network, gather critical data points for each entity, and implement monitoring systems. Data elements should include supplier capabilities, capacities, locations, materials used, transportation modes used, critical equipment details, and other insights.
Companies must also identify single points of failure or dependencies across the network. Real-time tracking of inventory levels, work-in-progress status, and shipment locations enables early risk detection. Integrating supply chain data onto a common platform provides a consolidated view.
Most importantly, modern technologies like the Internet of Things (IoT), analytics, cloud computing, and artificial intelligence help boost visibility. Sensors track the conditions of shipments, assets, and facilities, while predictive algorithms flag anomalies.
Additionally, real-time monitoring and continuous tracking help identify potential issues well in advance so that prompt corrective actions can be taken. Generally, good visibility helps analyze risks across critical areas like sourcing, operations, and transportation and anticipate appropriate mitigation plans.
3. Conducting Risk Assessment
Comprehensive risk assessment allows companies to pinpoint vulnerable areas in their supply chain network. They must proactively evaluate and quantify potential exposures across key risk categories, such as demand fluctuations, supply disruptions, transportation delays, political instability, natural disasters, etc. These assessments should be conducted periodically and when circumstances change.
A structured risk assessment methodology involves risk identification, analysis, and prioritization. Risks are identified through failure mode effect analysis, surveys and audits. Impact analysis evaluates the likelihood and severity of each risk, while prioritization classifies risks as high, medium, or low based on impact and probability.
The assessment also covers insurance program analysis for coverage gaps. Results provide visibility on ‘hot spots’ to focus mitigation resources to develop risk registers highlighting control actions and responsibilities.
Meaningful metrics continuously monitor the risks and effectiveness of programs. Continuous assessments strengthen preparedness against evolving threats.
4. Implementing Mitigation Strategies
Once risks are evaluated, concrete mitigation strategies are implemented to strengthen resilience. Mitigation tactics like dual/multi-sourcing, localizing suppliers, utilizing alternate transportation modes, increasing inventory buffers, and implementing demand forecasting capabilities and emergency preparedness plans can significantly reduce vulnerabilities.
Mitigation involves hardening the facility with preventive maintenance and upgrading it for natural disaster-prone areas. Strategies may also include diversifying production and distribution footprints to different geographies. Transition and business continuity planning help ensure operations continuity.
Insurance programs adequately cover residual risks that can’t be eliminated. Robust vendor/supplier qualification processes minimize third-party risks. Periodic reviews assess mitigation effectiveness with corrective actions.
5. Contingency Planning
Even with diligent risk management, some disruptions may occur. Contingency planning focuses on developing comprehensive plans to ensure smooth response and rapid recovery from unplanned disruptions. Backup sites and flexible sourcing options enable agility.
Crisis management teams trained in emergency procedures can swiftly swing into action. Well-defined incident command structures speed up decision-making.
Crisis simulations test different disaster scenarios to plug gaps. Contingency plans address alternative transportation scheduling, emergency sourcing activation, demand-supply balancing, communication protocols, IT disaster recovery, and more. They detail roles, responsibilities, checklists, response timelines, and escalation procedures.
Partners are also equipped to switch arrangements seamlessly. Early warning systems provide a lead time for planned contingencies. Post-incident reviews incorporate learnings to upgrade plans continuously. Speedy resolutions minimize adverse impacts on customers, costs, and reputation.
Conclusion:
Implementing all five pillars—visibility, agility, collaboration, contingency planning, and training—creates an adaptive, resilient supply chain security infrastructure. Continuous improvement across each element ensures preparedness for an ever-changing risk landscape.
Each pillar alone provides an adequate defense. An integrated approach embedding risk management from design to day-to-day operations builds a supply chain that can withstand disruptions and minimize their impacts. Proactive strategies prevent threats from becoming crises and thereby safeguard profitability, market position, and reputation among customers and stakeholders.
Mastering these five core aspects positions businesses at a competitive advantage through supply chain resilience in uncertain times.
Be the first to comment